With the growing global demand for energy conservation and environmental protection, energy conservation measures in the construction field have become the focus of policies in various countries. As one of the key technologies for building energy conservation, the Exterior Insulation and Finish Systems (EIFS) can not only effectively reduce building energy consumption, but also improve the comfort of the indoor environment and extend the service life of the building. In this system, hydroxypropyl methylcellulose (HPMC), as an important functional additive, plays a vital role. This article will delve into the specific application of HPMC in EIFS and its impact on system performance.
Basic Features of HPMC
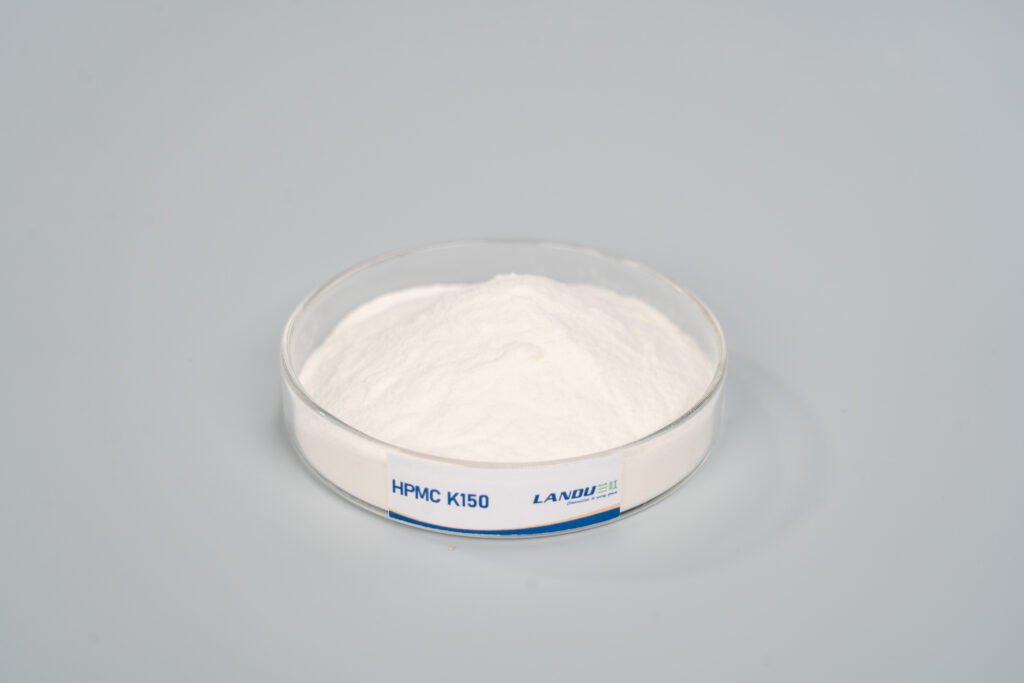
Hydroxypropyl methylcellulose (HPMC) is a non-ionic cellulose ether made from chemical modification of natural cellulose. HPMC is widely used in building materials due to its excellent physical and chemical properties. Key features of HPMC include:
Thickening: HPMC can significantly increase the viscosity of mortar and putty powder, making these materials easier to operate during construction and better adhere to the surface of the substrate.
Water retention: HPMC can significantly improve the water retention capacity of mortar and putty powder, prevent water from evaporating too quickly during the construction process, thereby ensuring sufficient hydration of the cement and improving the strength and adhesion of the material.
Lubricity and film-forming properties: HPMC has good lubricity, which can improve the workability of mortar and putty and make it easier to apply. At the same time, HPMC has film-forming properties, which can form a protective film on the surface of the material to increase its wear resistance and weathering resistance.
Stability: HPMC exhibits high stability over a wide pH range and is not prone to chemical degradation, so it can maintain its excellent performance under various environmental conditions.
Based on these characteristics, HPMC is widely used in EIFS and plays an irreplaceable role in many aspects.
Application of HPMC in EIFS
EIFS is usually composed of multiple layers of materials, including insulation layer, bonding layer, plaster layer and decorative layer. Among these materials, HPMC mainly plays the role of improving construction performance, improving material performance and extending the service life of the system.
1. Application in bonding mortar
Bonding mortar is the key material for fixing insulation boards (such as polystyrene boards, extruded boards, etc.) to the base wall. The role of HPMC in bonding mortar is mainly reflected in the following aspects:
Enhanced water retention
HPMC can form a stable hydration film in the mortar, delaying the evaporation of water, thereby allowing the mortar to have a longer operating time during the hardening process. This feature is important to ensure that high-quality construction of the mortar used in high temperature and dry environments.
Improve bonding strength
HPMC can increase the viscosity and thixotropy of the mortar, making the mortar easier to operate during construction and adhere more firmly between the insulation board and the base wall, thus improving the bonding strength of the entire system.
Improved workability
By improving the fluidity and flattening properties of mortar, HPMC makes construction more convenient and can improve construction efficiency while reducing construction difficulty.
2. Application in plastering mortar
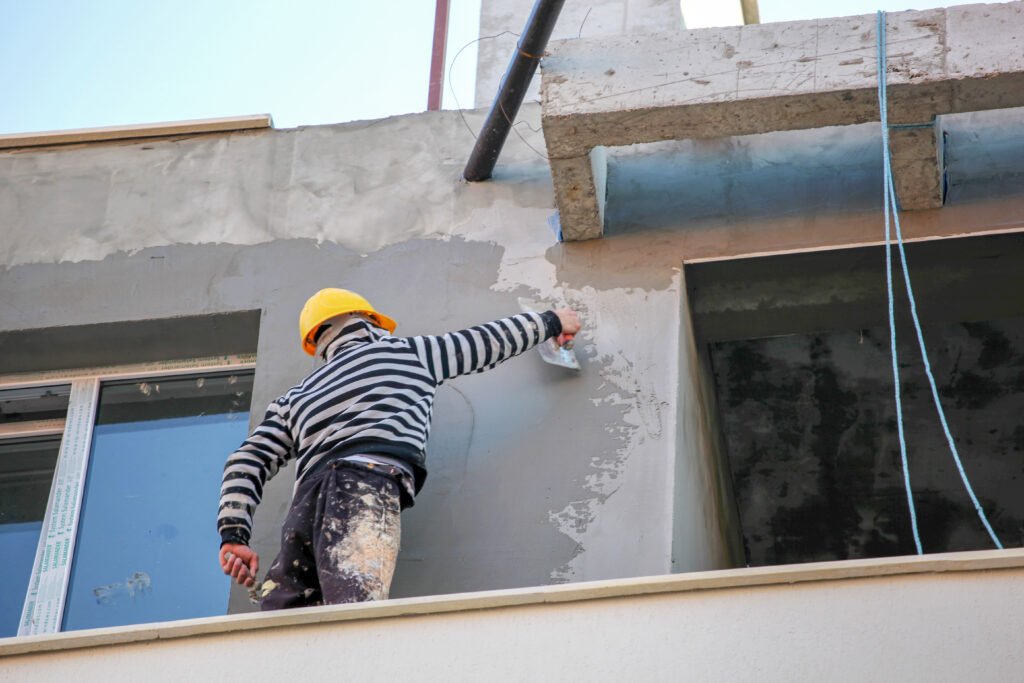
Plastering mortar is used to cover the surface of the insulation layer, protecting the insulation material and providing a base for the decorative layer. The role of HPMC in plastering mortar is particularly critical:
Enhanced crack resistance
By improving the water retention and flexibility of the mortar, HPMC effectively prevents cracking problems caused by excessive drying or temperature changes in the plaster layer, ensuring the long-term stability of the system.
Improve weather resistance
Plastering mortar must have good weather resistance when exposed to the external environment. The film-forming and weathering resistance of HPMC significantly enhance the mortar’s ability to resist erosion from the external environment, thereby extending the service life of the system.
Improve construction quality
HPMC makes the plastering mortar easier to apply and smooth during construction, reducing sagging and ensuring the smoothness and aesthetics of the plastering layer.
3. Application in putty powder
Putty powder is used for leveling and decorating exterior walls,which is an important material to ensure the beauty and durability of the decorative layer. The functions of HPMC in putty powder include:
Improved Fluidity and Ease of Application
HPMC enhances the smoothness and workability of putty powder during construction by providing thickening and lubrication. This allows for easier application, enabling the putty to quickly fill small wall defects and create a smooth surface.
Enhanced Water Retention
HPMC’s water retention capabilities prevent the putty powder from cracking or detaching due to rapid water evaporation during the drying process, thereby improving the overall surface quality after application.
Increased Durability
HPMC not only boosts the adhesion of putty powder but also enhances its wear resistance and anti-aging properties through effective film formation, ensuring that the decorative layer remains in excellent condition over tim
The Impact of HPMC on the Performance of EIFS
The application of HPMC in EIFS is not only to improve the construction performance of various types of mortars and putty powders, but also has a profound impact on the long-term performance of the entire system.
1. Improve the crack resistance of the system
EIFS is often affected by external factors such as temperature changes, wind pressure, and humidity changes during long-term use. These factors may cause cracks in the mortar layer, thereby affecting the insulation effect of the system. By enhancing the flexibility and water retention of the mortar, HPMC effectively reduces cracks caused by dry shrinkage or thermal expansion and contraction, significantly improves the system’s crack resistance and ensures the long-term stability of the system.
2. Improve system durability
The durability of the EIFS is key to ensuring its energy-saving effect. HPMC enhances the structural stability of mortar and putty powder by improving the water retention and weathering resistance of the material, and reduces material deterioration caused by changes in the external environment. In addition, HPMC also improves the UV resistance of the material and delays the aging process caused by sunlight, thus greatly extending the service life of the exterior wall insulation system.
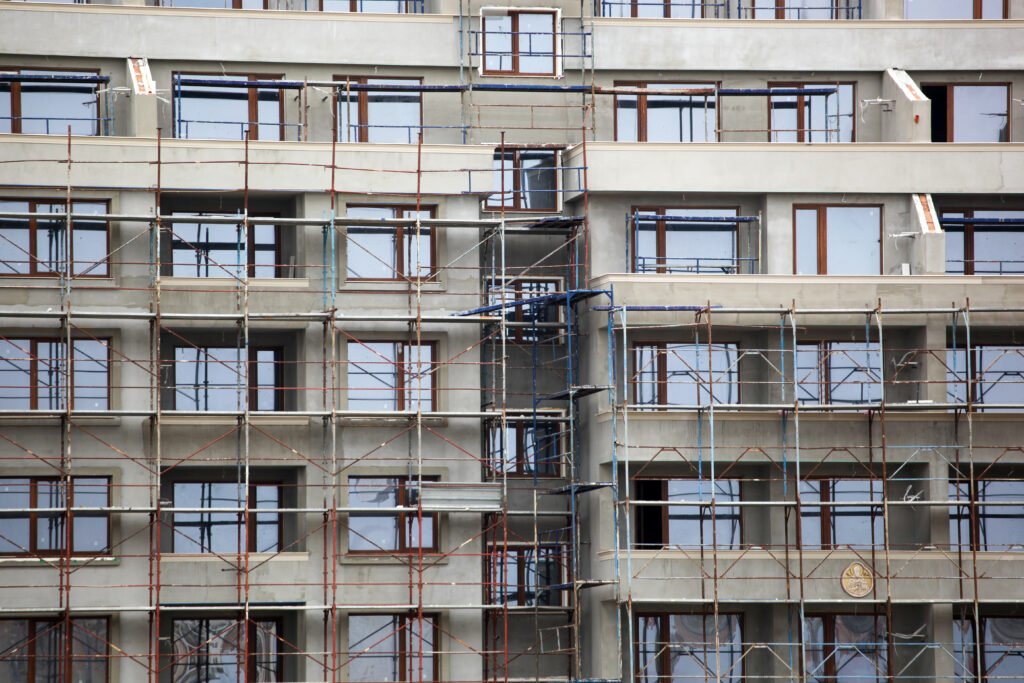
3. Optimize the energy-saving effect of the system
By improving the constructability and performance of various materials in the insulation system, HPMC enables the insulation layer to cover the wall surface more evenly, reducing the thermal bridge effect and optimizing the insulation effect of the entire system. In addition, HPMC can further improve the energy-saving performance of the system by increasing the density of the material and reducing air penetration.
The Future Development of HPMC in EIFS
With the continuous development of building energy-saving technology, the requirements for EIFS are also increasing. As a key functional additive, the future development trend of HPMC is mainly reflected in the following aspects:
1. Environmental protection
In the context of increasingly stringent environmental protection requirements, the production and application of HPMC must pay more attention to green environmental protection. In the future, HPMC’s production process will be further improved to reduce the emission of pollutants during the production process, develop more environmentally friendly HPMC products, and meet the construction industry’s demand for green building materials.
2. Versatility
As the performance requirements of building materials increase, the functionality of HPMC will be further enhanced. In the future, HPMC will not only be satisfied with improving basic functions such as water retention and thickening, but may also make breakthroughs in enhancing the fire resistance, antibacterial properties, and sound insulation of materials, thereby further improving the overall performance of the exterior wall insulation system.
3. Customization and intelligence
As the demand for personalized buildings increases, the application of HPMC will also develop in the direction of customization and intelligence. In the future, HPMC will make personalized adjustments to the formula according to different building environments and construction conditions to achieve the best application results. In addition, intelligent HPMC products may have automatic adjustment functions to automatically optimize their performance according to changes in environmental conditions, further improving the adaptability and energy-saving effect of the exterior wall insulation system.
Conclusion & Cellulose Ether Manufacturer - LANDU
The application of HPMC in EIFS has greatly improved the construction performance and service life of the system. By improving the performance of bonding mortar, plastering mortar and putty powder, HPMC effectively improves the crack resistance, durability and energy saving effect of the system. With the development of the construction industry in the future, HPMC’s role in EIFS will become more important, and its application scope will also be further expanded.Development trend of HPMC will also focus more on environment protection, versatility, and customization.
As a leading cellulose ether and RDP producer and supplier in China, LANDU is committed to delivering top-quality HPMC, HEMC and HEC products and services. We provide expert technical support, complete after-sales service, and customized solutions based on customer requirements. Feel free to get in touch with us anytime if you need assistance.