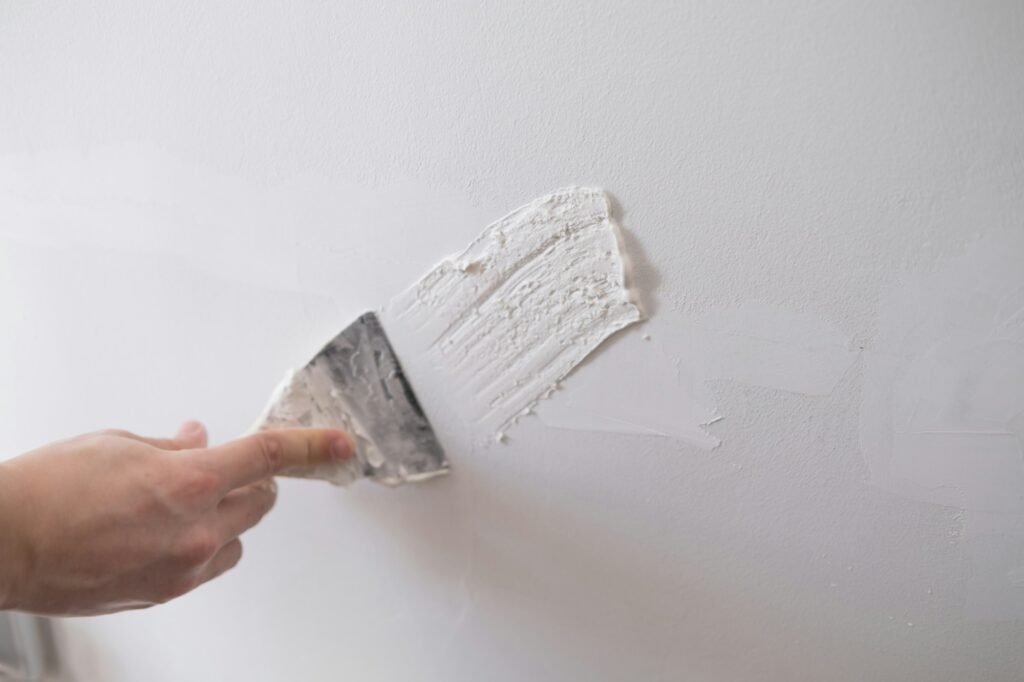
The application of exterior wall putty is widely and critically used in building painting projects. Exterior wall putty not only affects the aesthetics of the exterior wall, but also relates to the durability and quality of the whole building. However, in the actual construction process, the exterior wall putty often has various problems. These problems, if not solved in time, will affect the quality and effect of the overall project. In this paper, we will analyze nine common problems of exterior wall putty in the painting project and its solutions.
Problem 1 Chalking
Cause Analysis
- The poor-quality putty exhibits insufficient weather resistance and water resistance.
- The humid construction environment causes the putty surface to absorb excessive moisture, resulting in a chalking phenomenon.
Solution
- Adding high-quality additives such as HPMC, HEMC, and RDP polymer can enhance the weather resistance and water resistance and ensure the quality of the putty.
- Check the weather forecast before construction and avoid construction in humid or rainy weather.
- Keep the construction environment as dry as possibleand use dehumidifying equipment if necessary.
Notes
Name | Hydroxypropyl Methyl Cellulose (HPMC) | Hydroxyethyl Methyl Cellulose (HEMC) |
CAS number | 9004-65-3 | 9032-42-2 |
Other name | Hydroxypropyl Cellulose, Methyl Cellulose | Methyl Hydroxyethyl Cellulose |
Properties | water retention, thickening property, slip resistance, workability | thickening, adhesion, suspension, dispersion, emulsification, film formation |
Gel temperature | 60-75℃ | 75-90℃ |
- Redispersible Polymer Powder (RDP), with a CAS Number24937-78-8, also named Dispersible Polymer Powders, comprises polymer resins, additives, protective colloids, and anti-caking agents. It exhibits excellent hydrophobicity and weather resistance, playing a significant role in various construction fields such as tile adhesives and external wall insulation systems. International leading high-quality RDP companies include Wacker and Elotex.And LANDU is a Chinese Top RDP manufacturer and supplier.
Problem 2 Cracking
Cause analysis
- Excessive thickness of the putty layer can result in cracking due to uneven shrinkage during the drying process.
- Improper substrate treatment, such as not cleaned up or rough surface.
Solution
- Control the thickness of the putty layer, ensuring that each layer does not exceed 2mm. If multiple layers are needed, allow the previous layer to dry completely before applying the next one.
- Ensure the substrateis clean and smooth,if necessary, sand and clean it, and thoroughly wet the substrate before application.
- HPMC can enhance the toughness and elasticity of the putty, reducing shrinkage stress during the drying process. This effectively prevents cracks in the putty layer and improves the durability and lifespan of the coating.
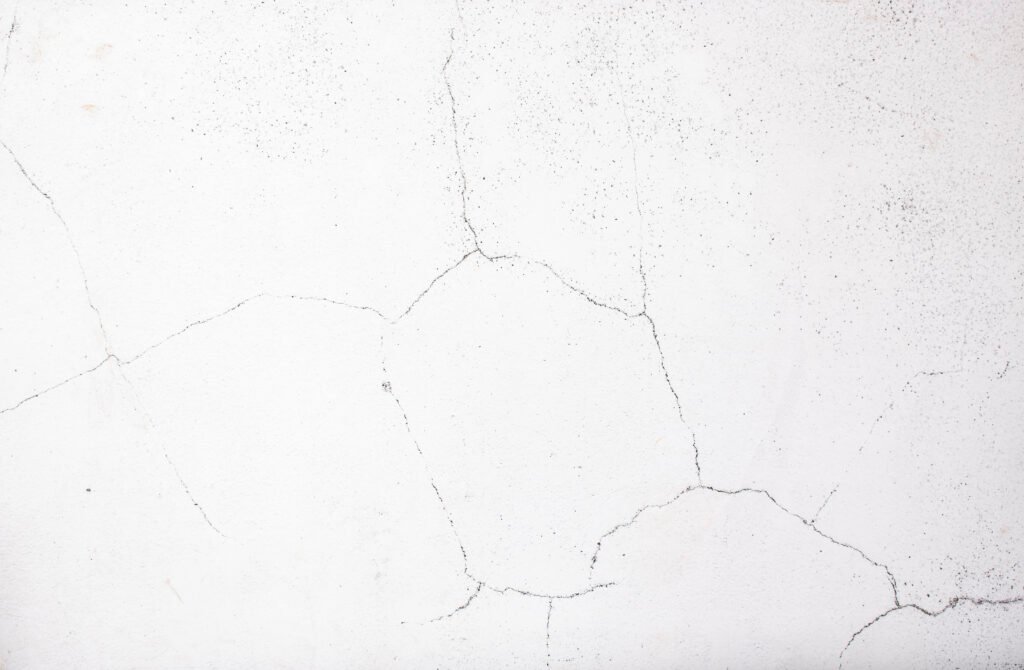
Problem 3 Blistering
Cause Analysis
- The presence of oil stains on the base layer or incomplete drying can result in air between the putty and the substrate.
- Not thoroughly removing air during constructioncan create bubbles.
Solution
- Thoroughly clean the substrate before construction to ensure that it is free of oil, dust and moisture.
- Use a scraper or trowel to level the putty during construction to avoid air trapped in the putty, and scrape several times if necessary to expel the air.
- The use of defoamerscan quickly reduce the air bubbles in the putty and improve construction efficiency. And after defoaming, the putty surface is more flat, which helps the beauty and quality of the coating.
Notes
- Defoamers are chemical additiveswhose main function is to quickly destroy foam that has already formed. It also prevents the formation of foam and keeps the process flowing smoothly, widely used in industries such as paints and coatings, pulp and paper, food processing, and pharmaceuticals.
- Types include oil-based defoamers, silicone defoamers, polyether defoamers, and so on.When using them, select a defoamer that iscompatible with specific processes and media, determine the appropriate dosage to avoid overuse, and ensure that the defoamer is well dispersed in the system for maximum effectiveness.
Problem 4 Shedding
Cause analysis
- Poor adhesion between putty and substrate, failingto firmly bond.
- The large temperature difference in the construction environment causes the putty layer to fall off under the influence of thermal expansion and cold contraction.
Solution
- Choosing to add HPMC,HEMC and other powder additives can improve the adhesion strength of putty, to ensure that the putty can be firmly bonded with the substrate.
- Avoid construction under extreme temperature difference conditionsand try to do putty construction under a moderate temperature environment.
Notes
- Adding HPMC and HEMC to tile adhesive can enhance the adhesive power of the adhesive and make the tiles adhere more firmly to the wall or floor, preventing loosening and falling off.
- In dry-mixed mortar, HPMC and HEMC can improve the bonding performance between mortar and substrate to ensure the construction quality and durability.
- HPMC and HEMC are used as thickeners and stabilizers in waterborne coatings and paints to improve the adhesion of coatings to the substrate, making the coatings stronger and preventing blistering and peeling.
Problem 5 Mildew
Cause Analysis
- Construction environment is humid, easy to breed mold.
- The putty itself has poor anti-mold properties and cannot resist the attack of mold.
Solution
- Improve the construction environment, keep dry and ventilated, and avoid long-time humidity.
- Select the putty with anti-mold performance, and enhance the putty’s anti-mold and anti-bacterial ability.
Problem 6 Color difference
Cause analysis
- Putty is not fully mixed, resulting in uneven color distribution.
- Different batches of putty are mixed, leading toinconsistent color.
Solution
- Mix the putty well before each use to ensure uniform color and texture.
- Try to use the same batch of putty, and avoid mixing different batches of putty.
Problem 7 Slow drying
Cause analysis
- The construction environment has high humidity and low temperature, which affects the drying speed of putty.
- Putty formula has problems, resulting in a long drying time.
Solution
- Increase the construction environment temperature, reduce humidity, and use heating equipment or dehumidification equipment if necessary.
- Choose fast-drying putty to shorten the drying time and improve the construction efficiency.
Problem 8 Pungent odor
Cause analysis
- Putty contains a lot of harmful chemicals, such as formaldehyde, benzene, etc.
Solution
- Choose environmentally friendly putty to ensure compliance with national environmental standards and reduce the content of harmful substances.
- Keep ventilated after construction to quickly discharge harmful gases.
Problem 9 Surface unevenness
Cause analysis
- The unskilled construction technique results in an uneven surface of the putty.
- Poor leveling of putty does not form a flat and smooth surface.
Solution
- Improve the technical level of construction personnel, conducting technical training and assessment.
- Select putty with excellent leveling abilityto achieve a smooth and flat coating surface. Incorporating HPMC can enhance the putty’s lubricity, making it easier to apply, lowering application resistance, and ensuring a smoother and more even putty surface, thus improving the overall aesthetic of the final coating.
Notes
- In addition to putty powder, adding HPMC to tile adhesive can improve its adhesion and workability, enhance the lubrication during operation, and avoid tiles moving or uneven.
- In paints and coatings, HPMC can improve its flowability, and reduce brush marks and uneven spraying.
- In the pharmaceutical industry, HPMC is used as an excipient to increase the sliding properties of pharmaceuticals, making tablets easier to handle during production and packaging, and improving the release characteristics of pharmaceuticals.
Conclusion & LANDU
There are various problems with exterior putty in the coating project, but as long as we find the root cause of the problem and take corresponding measures to solve it, we can ensure the construction quality and effect of putty. Choosing good putty products, high-quality HPMC, HEMC, RDP polymer, and other construction additives, and strictly controlling the construction environment and construction technology are the keys to ensuring the smooth progress of the exterior wall coating project.
As a leading cellulose ether and RDP producer and supplier in China, LANDU is committed to delivering top-quality products and services. We provide expert technical support, complete after-sales service, and customized solutions based on customer requirements. Feel free to get in touch with us anytime if you need assistance.